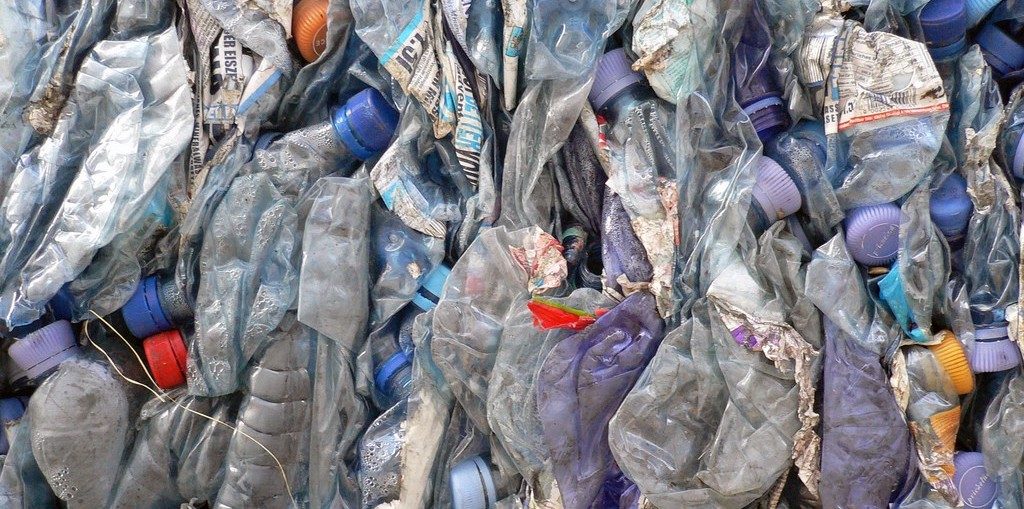
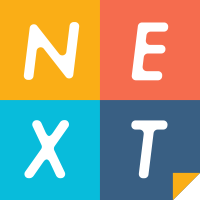
3D printing promises to be the next revolutionary technology, and it’s not just about toys for hipsters. It could dramatically change the politics of supply chains, offering a chance to make on-the-spot everything from umbilical clamps in Haiti, to a baby vein-finder in Kenya or prosthetic limbs in Sudan.
But just as printers need ink, 3D printers need filament. You can’t make something from nothing.
As William Hoyle, the chief executive of the U.K. charity Tech for Trade, explained, the cost of materials for 3D printing is pretty high. “A kilo of PLA [a type of plastic that can be used for 3D printing] is about $25 or $30, but if you were to buy the same material in a place like Nairobi you might pay double that.”
Tech For Trade wants to see filament produced locally and spotted an opportunity with waste plastics. The company is working with a local Kenyan NGO to employ refuse pickers in the Dandora slum–a dump just a couple miles from central Nairobi–to collect, clean, and shred waste plastic ready to turn into filament.
More than 15 million people make their living as refuse pickers. Tech For Trade hopes it could support such workers and boost recycling, as well as build systems for locally produced filament. The company has even established the Ethical Filament Foundation, hoping it can do for 3D printing what fair trade has done for coffee.
It’s a nice idea, but at present it’s the technical (rather than ethical) concerns that are holding up the process. Matt Rogge, Tech for Trade’s 3D4D technical director, is working on this.
He explained that different types of plastic produce different types of filament. High-density polyethylene–shampoo bottles, for example–is relatively easy to convert into filament, but it’s difficult to print with because it shrinks more than other plastics as it cools. On the other hand, polyethylene terephthalate–the recyclable plastic that most drink bottles are made from–prints well but is brittle, making it difficult to spool as filament.
Another technical challenge is getting ahold of adequately clean plastic; impurities that make it into the filament cause problems with the print. “Any solid particle comparable to the size of the printer nozzle it’s going through–which is usually 0.4 millimeters–is going to give you a nozzle clog,” said Rogge.
Still, they are hopeful. Rogge, who is usually based in Seattle, has been out training waste-picker groups in Africa and Mexico–and not just around filament either. He’s also been showing local organizations how to build their own 3D printers using locally discarded electronic components, an idea pioneered by West African inventor Kodjo Afate Gnikou, who built the first 3D printer produced from e-waste in a workshop in Togo in 2013.
The cost of such a DIY 3D printer is about $100, said Rogge, which is far below the cost of a commercial one. This removes another barrier to entry, the high cost of equipment, and marks a step toward establishing the sustainable, local 3D-printing businesses Tech For Trade envisions: ones that can produce items as required by their communities, be those umbilical clamps, vein finders, or prosthetic limbs.

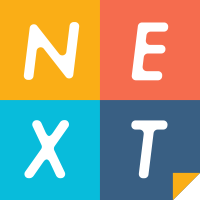
How We Get To Next was a magazine that explored the future of science, technology, and culture from 2014 to 2019. This article is part of our Design & Innovation section, which looks at new devices, concepts, and inventions that are changing our world. Click the logo to read more.