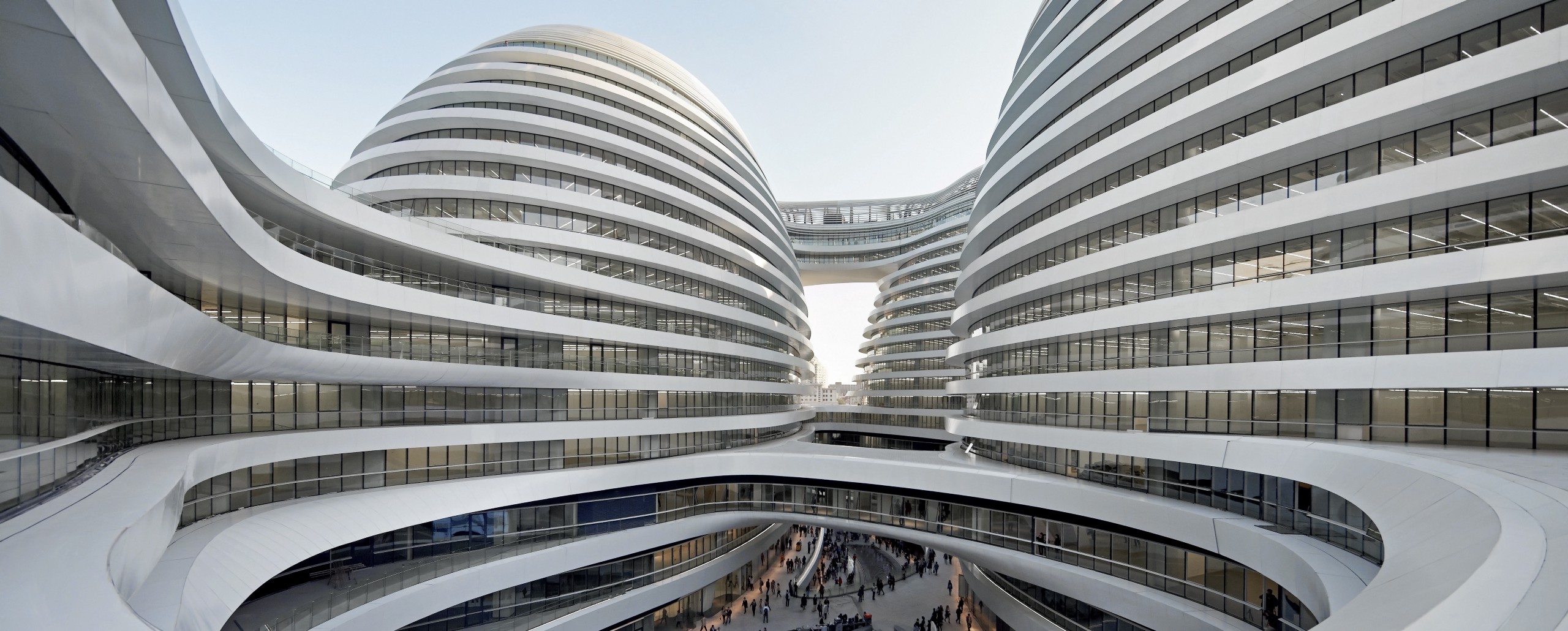
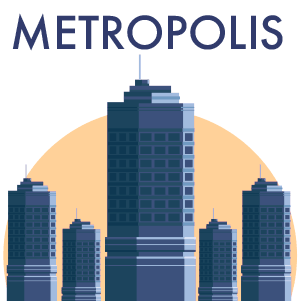
Thinner, lighter, smoother, and curvier than ever before–those are the cities of the future, thanks to the discovery of new building materials and the creative repurposing of traditional ones.
The architecture of large, expensive buildings has always been determined by artistic boldness, tempered by the limits of design and engineering. Now those same influences apply to smaller buildings like our own homes, whether in houses or tower blocks. Our priorities are changing. There’s more urgency for new buildings to be practical first and foremost–leaving a small environmental footprint, while staying warm in the winter, cool in the summer, and as light as possible all year round.
Concrete was the defining material of 20th-century modernism and suited the contemporary movement’s fondness for straight lines and symmetry. Later, advances in engineering made it possible for architects like Frank Gehry and Zaha Hadid to sculpt increasingly more extravagant buildings that are as much artistic expression as they are architecture.
Which materials will define the look of 21st-century cities?

Smart glass
No matter the variety, this should make it overall much easier to control how natural light works inside buildings. There are actually several different kinds of “smart” glass: One type is self-cleaning, its surface finely coated with a micro-scale non-stick coating; others use a UV-activated catalyst to break down the oils in grease marks into carbon dioxide and water.
Other types can be solar-sensitive, meaning they respond to changes in sunlight and temperature to darken (just like photochromic sunglasses), reducing glare and better controlling internal temperatures. In photochromic glass, the energy from sunlight knocks its atoms out of ordered “stacks” with gaps that let through 75 percent of light, into disordered, random positions that only let 25 percent of light through. It doesn’t have to be passive, either. It’s totally possible to control it directly in new electrochromic materials, which are activated by running a current through them, darkening slowly over five minutes to cut out up to 50 percent of light. As with the solar-activated glass, the current causes reversible structural changes.
The same principle can also be used to make glass that frosts up instead of tinting, offering privacy in places like offices or bathrooms without compromising access to natural light, as shown in the video above.

Daylighting
One way to use less energy is to make better use of natural light, instead of developing new artificial kinds.
Engineers have started doing precisely this in some buildings by directing natural light through shafts using reflective slats. It’s called daylighting, and it not only makes lighting cheaper and uses less energy, but it also provides a whiter, cleaner natural light that might decrease incidences of seasonal affective disorder (SAD) or short-sightedness.

Fantastic new metals
Metals can also adapt to new challenges. No complex chemistry or amazing new elements are needed either–we can change how metals behave simply by changing their structure.
Being able to make stronger, more efficient structures is vital in a world where many cities need taller and taller buildings as their populations grow and densify. But expanding upward comes with engineering challenges: Skyscrapers will need to become lighter and better dampened, particularly in areas where there might be earthquakes. Luckily, there are materials–called metal sponges–that can provide strength and rigidity, absorbing energy to prevent a building from swaying, while also soundproofing and insulating it.
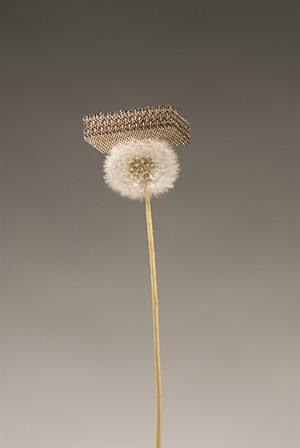
In 2011, researchers created a new metallic sponge they described as a “microlattice” by electrolytically depositing metal onto a polymer framework, which afterwards gets etched away. It created a three-dimensional porous metal matrix of interconnected metal tubes, with each tube only a thousandth the thickness of a human hair, or 100 micrometers across.
This microlattice is the lightest known solid building material. It’s 99.99 percent air, with a density that is 0.9 kilograms per cubic meter–that’s only 1.76 times the density of air itself. Early types have been made of nickel, aluminum, or steel, but any metal can be deposited onto the framework, making it flexible to incorporating other properties like electrical conductivity.
These are a relatively new development–and haven’t actually been used in buildings yet–but the aeronautic industry already has plans to use these metals in plane construction. They’re going to attach thin sheets to the surfaces of the sponge, forming a sandwich-like structure. The best sponges recover their shape entirely after being compressed to less than half their size, meaning they can be used as fantastic shock absorbers.

Composite materials
Not everything needs to be made of metal. With so many lightweight non-metallic materials already used to design aircraft, turbines, and yachts–not to mention the continued use and improvement of historically common building materials like wood–architects are keenly exploring alternatives to metal for buildings of the future.
Lighter buildings can be less expensive and take less time to construct, especially if the reduced weight is concentrated near the top. Although metallic sponges might look like a good way to lower the weight of a building in places, metals also have another problem: They expand when they get warmer. For now, most skyscrapers include a steel frame and can cope with expansion and contraction, but in the future it could be a limiting factor in designing new construction methods.
One possible solution comes from changing the geometry of a building, which also changes the way it distributes force. Monocoque buildings are curved and load-bearing through the outer skin, like an egg or an airliner. When buildings constructed this way expand and contract, it doesn’t compromise them quite as much as ones that bear their load through a frame built into a foundation.
The problem here, though, is that freeform shapes like eggs are very difficult to make from metals. Using composite materials is the solution–materials made from a mixture of different things. This gives them the enormous advantage of being moldable in many cases, their shapes worked to a high degree of accuracy by including detailing like filigree from the start. They can even be connected in new ways, unlike traditional heavy metal materials that require messy welding, especially when it comes to time-consuming detailing.
When Dubai architecture and engineering firm Affan Innovative Structures built Sidra Medical and Research Center, it combined Dow Chemical’s existing Voraforce TF epoxy with carbon fibers to essentially create a more sophisticated version of fiberglass–but one that is both 85 percent lighter than steel and yet twice as strong. Its light weight means that the roofs and wall panels built using it need far less support, enabling new architectural forms, but it’s also extremely resistant to expanding and contracting in heat, a crucially important trait for a desert building.
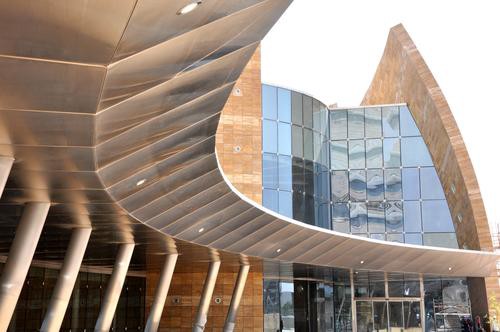
This is typical of what’s called “upcycling,” where waste materials are reused to make new ones, particularly composites containing plastic. One example is plasphalt road surfacing, which uses ground-up plastic waste in asphalt mix. It’s much more durable than normal asphalt, thanks to a strong chemical bond between the emulsifier and plastic, stronger than the one formed with the usual mixing material of sand.
The properties of a composite material can also be tailored to what’s needed. Their structural integrity normally comes from overlapping fibers, usually made of glass, carbon, or boron, though some also use wood-based fibers. These are set into a resin–a thermosetting plastic like acrylonitrile-butadiene-styrene (ABS), which is normally used to make climbing helmets.
Some composites use wood-based fibers combined with a polyester or polypropylene resin. These carbon fiber composites are tough, chemically resistant, and have a very good strength-to-weight ratio, accepting around 2,000 MPa of tensile force–about a fifth that required to turn carbon into diamond. They’re usually no more than five to 10 micrometers in diameter, comparable to the thickness of a spider’s web, and since they make up half of the mass it lends these materials the attractive appearance of woven fabric.
It also means that, like fabric, they can be made into thin sheets. Carbon fiber composites can come in sheets of between 20 to 40 millimeters thick, simultaneously saving space and allowing for strong, interesting shapes. In the future, though, those fibers might be made of graphene or carbon nanotubes, or one atom-thick layers of graphite rolled into long tubes. These are incredibly light, exhibit unique electrical properties, and measure the highest tensile strength of any material up to 63 GPa (that’s 630,000 times atmospheric pressure). They are more durable and adaptive than Kevlar, lighter and more flexible. Embedded in plastic, these materials can be shaped into lasting structures that don’t expand or deform on warm days, although they do need flame retardant coatings due to their wood content.
Some composite-like materials are less impressive for their strength than their appearance–like newspaper wood, a fancy kind of papier mâché made from resin-coated newspapers tightly rolled into logs then cut up into planks, developed by Dutch firm Vij5. Ink from the newspapers creates a grain affect and the planks can be sized up to the width of an open newspaper. Just like any other wood, newspaper wood can be sanded, milled, coated, and varnished. Much of the strength of this material is based on the strength of the glue. Newspaper wood uses solvent-free, plastic-free, water-based, organic glue, but a non-organic one might make it stronger.
This is another trend, with some designers reclaiming the use of wood as a building material, using glue to cross-laminate and significantly strengthen softwood timber. Buildings of 10 and 14 stories in Melbourne and Bergen, respectively, have been constructed primarily from laminate woods; the way they’re glued together gives them an entirely unique and new style of wood grain.
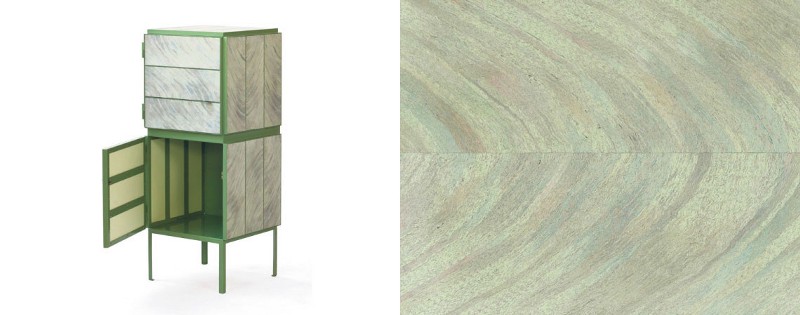
They don’t have to be radical new types of glue, either, dreamed up in a lab–many natural glues are just as good, be they derived from processed wood or tapped as sap from acacia trees. Or even made from foods such as starch and casein, and (in perhaps the more traditional way) from animals like hoof glue.
There’s more to glue than just keeping composite materials together, though. Our future houses, centers, and tower blocks are likely to be entirely glued together. We already have planes and appliances held together with glue, and architecture will be next. While today carbon fiber panels are unnecessarily bolted as well as glued together (the glue is usually stronger), we are growing more confident in “invisible” chemical adhesives.

So now picture this future city. We will have shafts and daylighting slats to keep our offices naturally lit, buildings that stay warm when it’s cold and cool when it’s hot. There will be no bolts or screws in view and everything may be curved, including the windows. The surfaces will be smooth or have a woven look–both alien and familiar–and the walls will be thinner and stronger at the same time. New skyscrapers will push the limits of height. On a sunny day, you’ll be able to walk through our cities seeing only the black-eyed reflections in dimmed glass; but on duller days, you’ll still be able to spy on your neighbors through the same window pane.

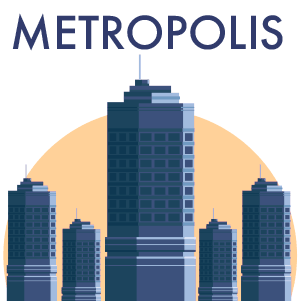
How We Get To Next was a magazine that explored the future of science, technology, and culture from 2014 to 2019. This article is part of our Metropolis section, on the way cities influence new ideas–and how new ideas change city life. Click the logo to read more.