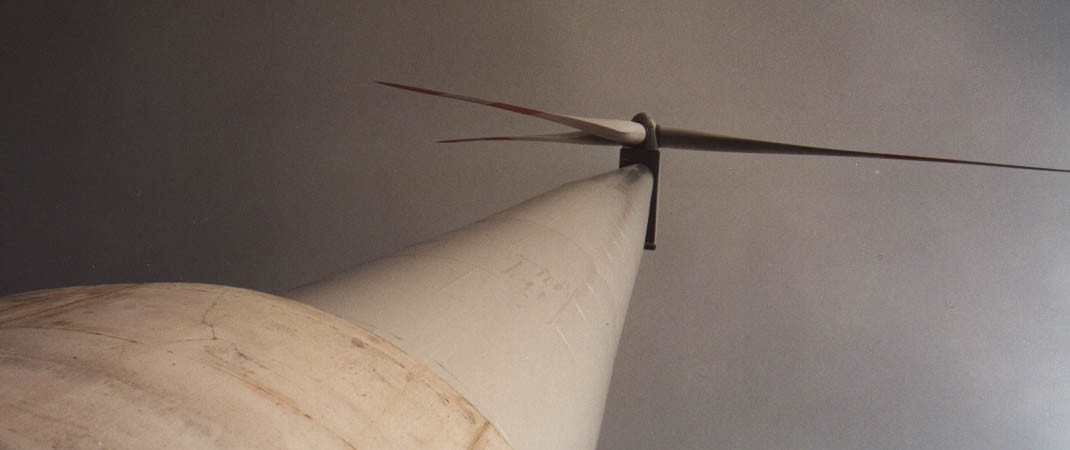
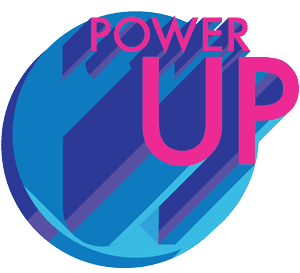
There is no single best design for a wind turbine. A three-bladed turbine is most common, and just about wins aerodynamically speaking, but the rarer two-bladed structures can often work more efficiently. Turbine designers have a range of issues to consider. What’s the intended power and location? What speed should it run? How noisy can it be? How big? Should the blades be upwind or downwind of the mast? Should they be fixed or twist to adjust power?
Technologies are never developed in a vacuum. Technical decisions are shaped by designers’ experiences. If we want to know why most wind turbines still have three blades, we could blame the Danes.
As recently as a decade ago, Danish firms dominated the international wind power market. They control over 20 percent today and the Danish company Vestas is still the world’s largest wind turbine manufacturer. So the “why” question is one of history, industrial structure, and funding.
Before regional and national grids were extended into the countryside, wind turbines were an important source of rural electrical power. In Denmark, scientist, inventor, and educator Paul la Cour had been experimenting with wind power since the 1890s and was instrumental in founding the Danish Wind Electricity Society in 1903. His design for a wind power DC electric generator soon spread throughout rural Denmark via training courses he ran for electricians.
After WWII, la Cour’s former pupil Johannes Juul began to investigate the possibility of building an AC wind turbine that could deliver power to the grid. Juul’s first experiments were downwind two-bladed designs, which had the advantage of automatically turning into the wind. But the choppy airflow behind the turbine mast caused multiple blade failures. He switched to an upwind design with active steering into the wind and, at this point, switched back to three blades, as he could rely on cross-bracing between the blades for lateral strength. He also added a feature that accounted for when the turbine sped up in high winds–the airflow over the blades broke down, meaning they’d slow again.
In 1957, Juul built a 200-kilowatt turbine at Gedser. It ran reliably for 10 years, though the unit-generating cost was higher than coal or oil. This design set the standard configuration for Danish wind turbines for the next three decades.
The oil shocks of the 1970s inspired many more to look toward wind power. The United States and Germany both invested in large-scale, government-funded research programs to develop wind turbines. The majority were aimed at developing megawatt-class turbines, developed by aerospace contractors. They had advanced aerodynamics, sophisticated controls for the twin blades, and lightweight structural design. But in practice, the aeronautical engineers had underestimated how different the turbulent airflow around a turbine was from the flow assumed by their theories, which had been developed for airplanes. Their high-powered lightweight designs were plagued by mechanical and structural failures. Many ran for only short periods, if at all.
Denmark also funded more turbine research, as the national electricity utility built a handful of turbines adapting Juul’s design. However, far more important was the support the country offered to small-scale craft producers. These used reliable, off-the-shelf parts–bits of trucks for example–to produce designs similar to scaled-down versions of the turbine built at Gedser in the late 1950s. As the power generated was still more expensive than the grid, they were arguably idealists’ versions.
In the late 1970s, when the Danish government introduced subsidies for wind turbines, producers of agricultural machinery stepped in to meet demand, purchasing the designs and patents of wind pioneers. Equally important was the creation of a national turbine test center at Risø. In order to qualify for tax credits, turbines had to be approved by the center, which quickly became a hub for sharing tips and knowledge (including which kinds of truck axles were best for building your turbine). The station’s engineers translated academic engineering theory into the kind of design information useful to the craft producers. Together with the Danish Wind Turbine Owners Association, they provided a useful grassroots exchange for cross-fertilizing design ideas, in contrast to the insular high-tech companies operating elsewhere. The resulting Danish design kept most of the features of the Gedser turbine, including its weight and reliability, but improved on its efficiency.
In the early 1980s, generous state tax incentives in California led to a “wind rush” and Danish producers managed to capture a large part of the American market. Over the decade, the Danes continually increased the power of their designs in stages, from 55 to 500+ kilowatts. Though changes to the California wind subsidies caused a number of those producers to go bankrupt in the late 1980s, the consolidated survivors are still the largest wind power manufacturers in the world, producing the most reliable turbines. Vestas’ latest design is projected to produce eight megawatts of power–and not a truck axle in sight.

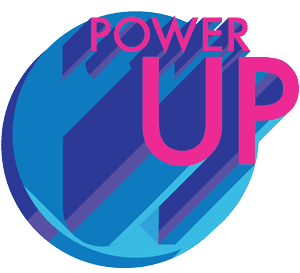
How We Get To Next was a magazine that explored the future of science, technology, and culture from 2014 to 2019. This article is part of our Power Up section, which looks at the future of electricity and energy. Click the logo to read more.